A heater hose is a kind of rubber hose that you can find in almost all vehicles with combustion engines. Its primary purpose is to pump the coolant of the engine over the core of the car heater. You can also use a mold heater hose for different shapes and purposes. But the question is how to mold a heater hose?
Most manufacturers heat the additional length they’ve determined and cut it off or bend for molding in different sizes and shapes. Molded Heater Hoses replace OEM refrigerant hose in pertinence where a small diameter (1 inch or smaller) molded hose production line is required.
Want to know more in details, please stay with us till the end of this guide.
How to Mold Heater Hose – Step by Step Guide
Molding and bending heater hose is a series of instructions. Here we explore the process.
Step 1: Choose the Required Length
First, you have to delimit the hose length as per as we need. You can do it simply by running a long piece of wire along the path you want to take and attaching it to the accessories you are about to slide and place.
Now, be sure to lengthen the wire to accommodate the hose length you want to put on the fitting. You will need a cable stock along the entire hose length, which you will have to run and slide over the engine mounting nozzles.
Step 2: Slide the Heat Shrink Tubing Over the Nozzles
Having cut the wire stock to the desired length, you must determine the desired heat shrink tubing to slide over the eng/rad nozzle. Suppose you need to put 3/8 “to slide on it. Then take a precision knife and cut off most of the 3/8 inch of wire around the edges.
Don’t cut them completely, and you have to keep them on the wire so that the heat shrink tubing ends don’t go through the heatsink nozzle. Now, remove those outer plugs later. It will keep the hose ends hollow and allow them to slide over the rad/eng nozzles.
Step 3: Cut Heat Shrink Tubing
Then cut a portion of the heat shrink tubing into a similar length as the wire you’ve just made. Now, put the heat shrink tubing on the wire stock, plus shrink it. Be sure to nail it to the pallets only at the back and on both sides, not at the front.
Step 4: Mold and Bend the Hoses
Then you have to bend in the hoses. Just twist the hoses to the desired shape and heat them over the candle. After you’ve heated both sides of the bend, submerge it in cold water, and the hoses will keep the bend on their own.
If you find a crease in the heat shrink, heat it over the wax, holding the curve with your fingers, and it will disappear. Submerge the hot-tubbing in cold water again to maintain flexion.
The great thing about using the wired material is that it doesn’t shrink like a hollow pipe. In this way, the hose retains its ideal round shape on bends.
How to Mold and Bend Heater Hose Without Kinking?
I tried to mold and blend the heater hose without kinking. But, it was too heavy and challenging to work in this way. The cord works like a fantasy. Explore the process!
- When you have folded the hose the way you want, just remove the pieces of wire from the hose ends.
- Then cut the heat-shrinkable tubing that has gone through the wire and shrinks more petite than the wire. These small heat shrink tubing pieces will grip the end of the hose, making it difficult to remove.
- After that, take a wooden screw and twist it to the hose center at the end you want to remove. Insert it tightly, and then just pull it out like a bottle of wine!
- The hose now has hollow ends at each end. Also, you can slide it over the eng/rad nozzle.
- Now make the final adjustments to the shape of the hose.
- Just fit it to your model, execute final shape adjustments and glue it on the rad/eng nozzles. Finish off with the 1/16″ strip of aluminum tape for resembling a hose clamp. It’s done!
Things to Remember:
- Do not flush the hollow hose ends. This will shrink the heat tubing, and you may not slide it over the rad/eng nozzles as you intended.
- If you want to warm up the ends again, insert a brass tubing piece of a suitable diameter onto the back and heat according to your preference. Don’t forget to plug out the end plugs before this procedure.
- The brass tubing prevents further shrinkage of the heat shrink tubing. Ensure to chill it in cold water before lifting the brass tube. If your heat shrink tube is still warm, it may shrink after pulling out the brass tubing.
Best Molded Heater Hose
- Dayco Molded Heater Hose
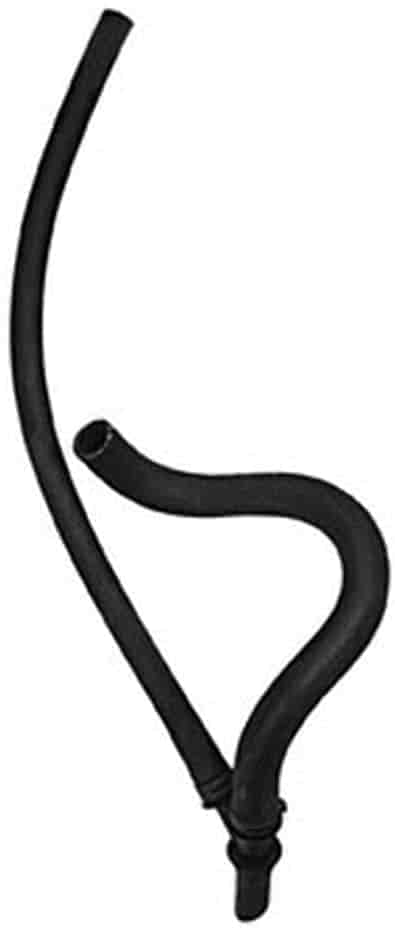
Keep the coolant warm by circulating through the Dayco radiator hoses. These hoses contain synthetic EPDM to provide higher durability in salt, oil, dirt, coolants, mud, and components.
The inner tube of the mold base for the Dayco Heating hose contains woven rayon for maximum power and explosion protection. Also, it eliminates the requirement for multiple hose connections and clamps. You can use them to ensure correct installation and operation.
- Gates 90 Degree Molded Heater Hose
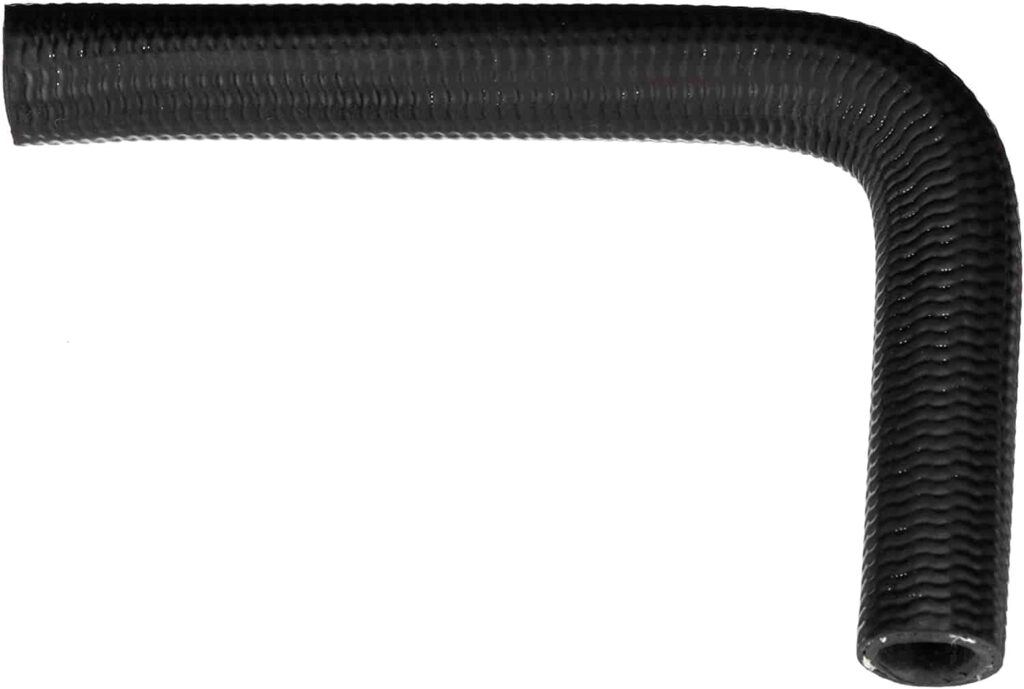
Sometimes it may be challenging to find hoses that fit easily into your assemblies. Gates molded heater hose makes it easy to replace existing tightly bent hoses. Their official 38 sizes are suitable for thousands of purposes and are highly durable.
Moreover, the Gates 90 degree heater hose is resistant to electrochemical destruction and water penetration. Also, it is compatible with coolant, water, and air systems.
Final Verdict:
The molded hoses are lightweight, flexible, and look like rubber hoses as they have rubber. You can find heat shrink tubes in different colors to enrich things a bit.
This small hose bending process is simple, quick, and affordable. I don’t think it may take more than 15 minutes to bend and mold a regular hose.
Remember that the bent hoses are flexible and soft. And so you may adjust it without overheating. If you want to make a BIG adjustment, warm-up is not a problem. Then you will get exactly the shape you want.
If you put the hose on the rad/eng nozzle, you have to end up with a flake hose on which you can see the diameter. So it looks almost like a radiator hose.
Well, that’s all about our “how to mold heater hose” guide. If you have any questions, feel free to ask.